不同设备用材与其化学成分、金相组织和热处理状态密切相关;设备的安全又与其中的缺陷相关联。一. 压力容器用钢中的金相组织及其性能1. 铁素体(F) 铁素体是有少量的碳和合金元素溶于体心立方晶格α-Fe中形成的固溶体(碳以间隙状态存在)。由于铁素体中碳很低,因此它具有良好的塑性、韧性,但强度(约为250~300MPa)和硬度(约为80~100HB)较低。 锅炉压力容器用的低碳或低合金钢组织多为F+P,例如:20g;16MnR、09MnNiDR等;0Cr13为铁素体不锈钢。2. 渗碳体(Fe3C) 它是铁和碳的化合物,硬(约745~800 HB)而脆。它与铁素体形成的机械混合物称珠光体。Fe3C的多少、大小、形状等对钢材性能影响很大,若其颗粒细小、弥散度大,可起到强化基体的作用;若呈粗大的片状或网状,会造成材料脆化。3. 珠光体(P) 它是奥氏体冷却过程中共析反应的产物,铁素体和Fe3C片形成交替排列的层状结构。高温回火时Fe3C成粒状均布于铁素体内。其强度和硬度较高(约200~280 HB),塑性较低。珠光体是在较高的奥氏体化温度(在A1~650℃)下形成,属扩散型的相变。4. 奥氏体(A) 它是碳和合金元素在面心立方晶格γ-Fe中形成的固溶体,大多数钢材在高温时才存在奥氏体(钢材热压时,要求达到此状态),而一些不锈钢室温时为奥氏体。它有较高的韧性和塑性(δ5为40~60%),强度和硬度(约170~200HB)适当。18-8、18-12等不锈钢经固溶处理后组织为A;这类钢在热轧状态或经一定量的冷变形会出现F 成为A+F,这是不希望的,应重新固溶;而2205双相不锈钢有约50%的A和F。5. 索氏体 (S) 它又称为细珠光体。当奥氏体转变的冷却速度较快时,比珠光体形成的温度更低的条件下(650~600℃)得到的铁素体与Fe3C薄片状混合物。高温回火后Fe3C呈粒状称回火索氏体,它有很好的韧性和适当强度,硬度HRC约30(HB~300)。6. 屈氏体 (T) 它又称极细珠光体。当奥氏体在快冷时,比索氏体形成温度更低的条件下(600~550℃)转变为屈氏体。中温回火后称回火屈氏体,其硬度较高HRC约为38(HB接近400)。7. 贝氏体(B) 贝氏体的转变温度范围介于珠光体和马氏体之间,当奥氏体冷到低于珠光体但高于马氏体形成温度(550℃~Ms),贝氏体既可在等温冷却过程中,也可在连续冷却条件下形成。在此温度下,铁和合金元素已不能扩散,而碳原子尚能扩散,属半扩散型的相变。因此,其转变兼有珠光体和马氏体的特征,但又有区别。 与珠光体相似的是:有碳的扩散,且生成铁素体与Fe3C的混合物;但其晶格改组是通过切变方式,这又与马氏体的共格转变相似。 在较高温度(600~350℃)形成的为上贝氏体,其显微组织呈羽毛状;在较低温度(350℃~Ms)形成的为下贝氏体,其显微组织呈针叶状。在低合金钢焊接接头中,还常出现粒状贝氏体也称M-A相。 贝氏体(特别是下贝氏体)具有较高的强度和较好的韧性,一些设备用钢(如13MnNiMoNbR、2.25Cr-1Mo),通过热处理以获得这样的组织。 低合金钢焊接是在非平衡状态下进行,焊缝金属组织转变中的P转变受抑制(特别是含微量Ti、B等),从而扩大了F和B的转变,在HAZ更加突出。8. 马氏体(M) 在连续冷却过程中,一般冷到Ms点以下(在此温度下,碳原子无法扩散),发生无扩散的切变型转变(Ms~Mf),碳在α-Fe中呈过饱和状态。属非扩散型的相变。 低碳马氏体呈板条状,也称马氏体束或马氏体领域,其束与束之间具有一定的夹角,一般呈60°也有呈90°。低碳及低合钢淬火后可得到板条状马氏体,在低合金钢焊接热影响过热区中有时也能见到。低碳马氏体具有较高的强度和较好的塑韧性,CF-62钢(07MnCrMoVR、07MnNiCrMoVDR)就是通过调质获得一定比例的这种组织,回火后为回火索氏体。高碳马氏体呈针叶状,它具有高强度、高硬度(HRC≥60)和低的塑韧性。 0Cr13、0Cr17等不锈钢和18-8等A不锈钢中,若存在马氏体,会使钢材的强度和硬度升高,塑性和韧性及耐腐蚀性能降低,这也是不希望的。9. 魏氏组织(W) 亚共析钢在铸、锻、轧制、焊接和热处理时,在高温形成粗晶奥氏体。随后在较快条件下冷却,一方面先共析铁素体沿晶界呈网状析出;另方面其铁素体在奥氏体晶粒内沿一定方向以针片状或棒状析出,分布在珠光体基体上,这称为魏氏组织。魏氏组织是一种过热组织,会使钢的韧性、塑性降低,脆性转变温度升高。但只有奥氏体晶粒粗化,出现针状铁素体切割基体严重时,其不利影响才明显。10. 其它相(1)碳化物(Fe Cr)23C6、(Fe Cr)7C3 碳氮化物(CN、 C2N)(2)σ、R、χ等(富Cr的脆性相)(3)α'(475℃脆性)
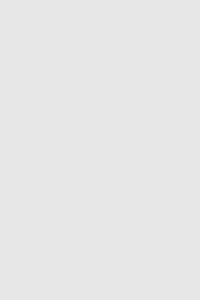
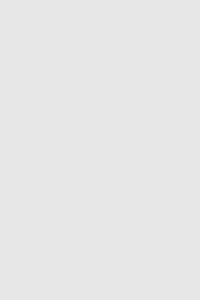
二. 压力容器用钢的几种热处理将钢材加热到一定温度经适当保温,然后以选定速度冷却以改变金属组织结构,从而获得所需性能的工艺称热处理。
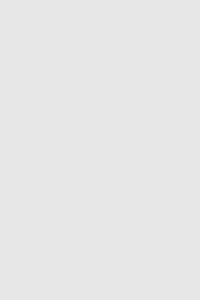
1. 正火 将钢材加热到AC3以上30~50℃奥氏体化经保温均匀化后,在空气中冷却,这称正火,也称常化。许多碳素钢和低合金钢通过正火可获得较细的均匀组织,强度和硬度有所提高,塑性和韧性也有所改善,使钢材具有良好的综合性能。 GBT150.2规定:用于壳体厚度大于30mm;用于其它受压件(法兰、管板、平盖等)壳体厚度大于50mm的Q245(原20g、20R)和Q345(原16Mng、16MnR)应在正火状态下使用。而16MnDR厚度6~60、60~120 mm要正火或正火+回火。2. 淬火 将钢材加热到AC3以上30~50℃奥氏体化经保温均匀化后快速(水冷或油冷)冷却,获得的马氏体组织。因过饱和溶入的碳原子引起铁素体晶格畸变(含碳量愈高,畸变愈严重),而具有很高的强度和硬度,塑性和韧性却很低。含碳量较高的工件,其马氏体转变往往伴随体积膨胀,会产生较大的内应力,若处理不当可能产生变形或开裂。3. 回火 淬火后形成的马氏体是不稳定的,通过回火使淬硬组织中过饱和的碳原子以Fe3C的形式析出,从而减少晶格畸变和降低内应力恢复钢的韧性。 回火是将钢材加热到AC1以下某一温度,经保温后在空气中冷却。通常采用高温回火(如500~650℃),其Fe3C聚合为弥散度较大的质点,与铁素体形成的混合物,称索氏体(S),其强度较高,塑性和韧性良好。淬火加高温回火也称调质处理。正火后也可高温回火,以消除应力和改善组织。4 . 退火 将钢材加热到AC3或AC1以上30~50℃,经保温后缓冷(随炉或在缓冷坑中),前者称完全退火,后者称不完全退火。退火的目的是细化晶粒、均匀组织,降低硬度、消除内应力,改善加工切削性能。对于焊接结构的去应力退火属于低温退火,加热温度在AC1以下(一般在600~650℃),去除焊接残余应力。 综上所述,压力容器用碳素钢和低合金钢的热处理状态有正火(N)、正火加回火(NT)、调质(QT)、退火等。三. 压力容器设备焊接或使用中的几种裂纹 所谓焊接裂纹是在焊接应力及其他致脆因素共同作用下,焊接接头中局部区域的金属原子结合力遭到破坏而形成的新界面所产生的缝隙。 人们习惯上按裂纹产生的原因、温度区间和性质来分类,如:冷裂纹、热裂纹、再热裂纹、层状撕裂和应力腐蚀开裂等。1. 冷裂纹(cold crack) 焊后,焊接接头冷却到较低温度时产生的裂纹称冷裂纹。一般情况,钢材的冷裂纹发生在马氏体转变点(Ms)以下或200℃(或150℃)以下。冷裂纹又可分为淬硬、低塑性脆化和氢致裂纹。 冷裂纹是焊接裂纹中最常出现的缺陷,一般说来,它是因母材的淬硬组织、焊缝金属中的氢含量以及拘束应力等因素的综合作用产生的。具有孕育期的冷裂纹称延迟裂纹。这类裂纹具有潜伏期,缓慢扩展期和突然断裂期三个阶段。一般认为:潜伏期和缓慢扩展期与氢的聚集和扩散有关,所以又称氢致延迟裂纹(delayed crack)。2. 热裂纹(hot crack) 在焊接过程中,当焊缝和热影响区冷却至固相线(铁—碳平衡图上的AE线)附近的高温区产生的裂纹称热裂纹。热裂纹又可分为结晶裂纹、液化裂纹和高温低塑性裂纹。 热裂纹是焊缝金属冷却、金属结晶时,由于低熔点共晶的存在或杂质在晶界的偏析,使金属高温延性或塑性变形能力不足以承受该区域的拉伸应变,从而造成沿晶开裂。热裂纹的产生原因主要取决于冶金和应力的因素。 结晶裂纹。焊缝在结晶过程中,在固液共存(铁—碳平衡图AC和AE线之间)温度以下,凝固的金属在收缩、残液补充不足,而低熔点共晶和杂质沿晶界形成一定数量的“液态薄膜”,在拉应力的作用下导致沿晶开裂。因为是在高温下开裂,其断口具有氧化色彩。 某些低合金钢、铝及铝合金、单相奥氏体钢、镍基合金等容易产生结晶裂纹。 例如:某公司炼油厂新建的制氢装置,下集合管(Φ1052 mm×26mm的15CrMoR)与其上的外接管(Φ168 mm×26mm的0Cr18Ni9Ti)采用鞍座式角焊缝连接。选用Ni≥67%的镍基焊丝(ERNiCr-3)氩弧焊打底、inconel 182焊条焊满。焊后经650℃×2h的热处理。试车中先后有89根外接管出现穿透和未穿透的裂纹。对镍基焊缝检验时发现:焊缝中有沿奥氏体树枝晶扩展的裂纹,且有气孔和夹渣;有的裂纹呈龟裂状。是典型的结晶裂纹。3. 再热裂纹(stress relief cracking)。 构件焊后在一定的温度范围内再次加热(SR处理或其他加热过程)而产生的裂纹称再热裂纹,又称消除应力(SR)裂纹。 一般认为再热裂纹的发生与钢材的沉淀硬化有关,只有那些能形成沉淀硬化的低合金钢、奥氏体钢和时效强化的镍基合金才会出现再热裂纹。 焊接加热时,邻近熔合线的母材被加热到1300℃左右,钢材发生晶粒粗化且钢中的合金碳化物溶于奥氏体。焊后冷却过程中被溶解的合金碳化物来不及析出,而在随后的SR处理(500~700℃)加热过程或高温运行期间,这些碳化物(V4C3、NbC、MoC等)在晶内弥散沉淀,从而晶内强化,使应力松弛时的蠕变变形集中于粗晶晶界,导致沿晶开裂。 还有晶界弱化说:即钢材在SR处理(500~700℃)过程中或设备高温运行时,碳化物(Fe3C等)呈片状或条状沿晶界析出;低熔点杂质和B、P、Sb、Sn、As等微量元素也容易偏析于晶界。当应力松弛时的应变超过晶界的塑性就会导致沿晶开裂。 也有研究认为:再热裂纹的产生主要取决于材料晶界高温强度的下降。焊接的一次加热过程中,既使奥氏体晶粒粗化,又造成奥氏体晶界杂质元素的富集,从而加速晶界脆化所致。再热裂纹是在焊后热处理或长期高温运行时,多数发生在熔合线以外的HAZ粗晶区。 例如:某公司两台07MnCrMoVR的 2000m3丙烯球罐。其设计压力:2.16MPa;设计温度:-20~50℃;规格:Φ15700×46mm; 2000年1月投运,2001年2月首次开罐发现:在球罐内、外壁分布200多条表面裂纹,以赤道带大环缝(WC)居多。现场经多次焊接修复,对环缝整圈几次热处理均发现不同程度的多处HAZ粗晶区或熔合线(FL)的沿晶开裂。最大裂纹长度达到2m,最大深度为20mm。经过返修,第一次SR处理后在WC环缝沿下熔合线乃有裂纹(以沿晶为主,局部呈穿晶)。有的部位甚至经水压试验后,在WC环缝沿下熔合线附近还有裂纹(总长约13 mm,呈沿晶扩展)。4. 应力腐蚀开裂(stress corrosion cracking) 金属材料在某些介质中,由于拉应力的作用造成的延迟破裂称应力腐蚀开裂。它的形成必须有介质、金相组织和应力这三要素在特定条件下的联合作用。它不一定在焊接接头上,也可发生在母材上。但由于焊接引起的接头残余应力因素无法避免,所以出现几率高的仍是焊接接头及其邻近母材。其典型的有:1)液氨容器的应力腐蚀开裂;2)含湿H2S容器的应力腐蚀开裂。 近年来,某公司发现LPG球罐的氢鼓包和开裂,这是因为介质未脱硫或脱硫不完全,属于湿H2S环境下的氢鼓包和应力腐蚀开裂。3)含苛性碱介质的应力腐蚀开裂;4)NO3引起的低碳和低合金钢容器的应力腐蚀开裂; 随着原料的重质化和劣质化,炼油厂催化裂化装置中的再生器先后腐蚀开裂。5)氯离子引起的不锈钢容器的应力腐蚀。 氯化物应力腐蚀开裂( ClSCC):最敏感的是含8%Ni的奥氏体不锈钢(如300SS系列,304、316等。5. 晶间腐蚀裂 在腐蚀介质作用下起源于金属表面并沿晶界深入内部,使晶粒间结合力损伤,严重时材料强度几乎消失这种现象称为晶间腐蚀。 不锈钢的晶间腐蚀通常用“贫铬”理论解释,即固溶于不锈钢中的碳在500℃~800℃加热(最危险的“敏化温度”为650℃左右),在晶界附近生成Cr、Fe23C6并沿晶界析出。由于碳比铬向晶界扩散快,形成碳化物所消耗的铬大量取自晶界附近,导致晶界贫铬。当铬降至低于耐蚀所需的极限含量(~12.5%)时,就出现晶间腐蚀。四. 工程实例(一)低合金钢设备(含复合钢板设备)1. 再生器开裂 某炼油厂的再生器先后开裂(投用4~12年),其主要技术参数: 设计及操作压力:0.3MPa;设计温度:介质为520~780℃,壳体<300℃;规格:Ф7m/Ф12m/Ф9m×24/30×49530mm。材质:16MnR;介质:油气、烟气、催化剂。(1) 检测情况1)9米段外壁沿下FL直边侧最长1.96米开裂。2)从外壁UT发现12米段H11横裂,扒开隔热层H9~H15七条环缝均有裂纹(H9、H11、H13、H15较严重),纵缝少。3)硬度测量(外壁)部 位HV平均值最高值
有裂纹处250~260300
无裂纹处200~210(环缝);190(纵缝)
BM160~170
4)金相:a.外壁:穿晶开裂是典型的冷裂纹;b内壁: ① 冷裂纹:沿下FL直边侧1米左右开裂; ② 应力腐蚀开裂:横裂、分叉。(2) 原因分析1) 30mm厚的16MnR在南方阴雨的冬季施工、不预热、不后热(符合JB/T4709)、不SR处理、其淬硬倾向大,焊缝金属中的扩散氢含量高。2) 采用半自动焊且焊缝长(Ф12米段,周长近40m,4个焊工每段10m)收缩应力大。3) K型坡口,应力集中大,均沿下FL直边侧开裂。以上具备了产生冷裂纹的条件(淬硬、氢含量以及残余应力),同时又促进应力腐蚀开裂(材料、介质、应力)。(3) 处理措施 该设备12米段七条环缝铲除(包括WM两侧BM上的裂纹),并将K型坡口改成不对称的X坡口,重新用J507焊接,预热,后热且经SR处理后投用;同时将内衬减少,使壳体的温度超过烟气的露点。2. 不锈钢复合钢板设备水压试验时爆裂 某炼油乙烯项目催化裂化装置改造中有三台塔器(见下表)由某公司制作。至2007年11月底,塔器制造基本完工。名称主体材料规格 /mm钢板数量/ t水压试验
吸收塔16MnR+
SA410SФ2800×(22+3)×54700全部131爆裂
脱吸塔Ф3400×(26/28+3)×40550全部125
稳定塔20R+SA410SФ3000/Ф3600×(20/24/28/36+3)×51050部分板材完成
分镏塔Ф5800×(20+3)×18190半台96
2007年11月26日吸收塔(设计压力2.15 MPa;设计温度70℃)制造完毕,其A、B类焊缝100%RT,符合JB/T4730-2005Ⅱ级,准备进行水压试验。11月27日晚封孔上水,11月28日上午采用工作压力为2~4Mpa的水泵开始试压。当日天气晴,气温约14℃。水温约为12℃。中午11:50左右压力表开始显示带压,下午1:00左右,当压力升至1.8Mpa时,该塔第22、23、24节筒体处突发性爆裂,裂口全部出现在本体上,形状不规则,纵向最大长度约3.7米,周向最大长度约1.8米。 对23、24筒节取样作化学分析和力学性能试验,成分正常(S:0.0055%、P:0.0125%),σb 535~540MPa;σs360~370 MPa正常,但16MnR的0℃的分别AKV分别为8、5、7;8、8、6;金相组织不正常,质保书中有11张钢板的0℃均AKV为31J。 对另外设备20R+410S(规格为20+3mm)的剩余材料取样做冲击试验,其三组冲击功平均值分别为30J、17J和8J(合格指标为27J);(GB 6654要求值,制造厂不怀疑,因属二类容器也不复验)。 复合钢板的质量问题比较复杂:有基材、复材的成分、性能及热处理状态;有爆炸复合后的消除应力热处理;有热成形后的热处理诸多问题。多台设备报废、退货等,给用户、制造厂、钢厂带来巨大的损失,索赔烦琐。 GBT 150.2的4.3.1和4.3.2分别为不锈钢-钢、镍钢-钢复合板应在热处理后交货,其交货状态要符合本标准对基材的规定。
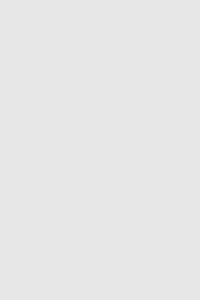
3. 不锈钢复合板设备水压试验后的点腐蚀 某公司制造环氧乙烷装置中的洗涤塔,规格为Ф5000×筒体(34+3)/封头(40+3)×88000mm,筒节为正火状态的16MnR+0Cr18Ni9(34+3)、封头为正火状态的16MnR+00Cr19Ni10(40+3)、塔内件为固溶状态的304不锈钢。产品分四段制造,复层酸洗钝化并经蓝点试验合格后在工地安装,环焊缝经酸洗钝化并经蓝点试验合格后进行水压试验(充水到放水历经19天)。此后不久,发现塔体内壁水渍流淌方向出现大量点状腐蚀,而封头和塔内件及焊缝腐蚀的较轻。(1)经水质化验表明:水中氯离子含量过高(50PPM),超过《容规》和GBT 150要求低于25PPM(25mg/L),奥氏体不锈钢不耐氯离子的腐蚀。腐蚀发生在排水后,水渍未清除干造成的;(2)不同含碳量、不同热处理状态的奥氏体不锈钢,仅不含Ti或Nb的正火状态含碳量较高的0Cr18Ni9表面腐蚀较重;而焊缝金属、固溶或超低碳的不锈钢腐蚀较轻;4. 焦炭塔不锈钢复合钢板上的焊缝裂纹 焦炭塔是延迟焦化装置中的核心设备,其工艺是将价值低的劣质减压渣油转化成价值较高的汽油、中馏分油和焦炭等,从而获得极大的效益。为防止塔上部含硫介质的腐蚀,从塔顶到泡沫层以下200mm用0Cr13(410S)复合钢板制造。 例一:某公司的焦炭塔:设计压力:0.38;φ5400×(20+2)/38/42mm;塔上部选材料为SB42+SUS410S的复合板(20+2)mm。中、下部为20g。基层用E4315焊条;过渡层E309-15;覆层E308-15。 1995年7月对其检验时发现:在主要靠近母材焊道的纵、环缝上均有沿晶扩展的裂纹。从其形貌特征判断,均为焊接热裂纹,在使用过程有进一步的扩展。这主要是焊接过程的质量控制不严。 例二:某公司新建的四台焦炭塔,壳体采用15CrMoR,其上部复合钢板为15CrMoR+SA410S;规格为Φ9000×40600×(22+3)/(24+3)/30~40 mm;复层的焊材为Ni182。 根据设计和规范要求,以火焰加热进行整体热处理,升温至690±14℃×2h后自然降温。在热处理后的PT检测中发现:焊缝及两侧复层表面有大量细小裂纹(长约10mm)及龟裂(直径约10mm~20mm)。 其裂纹类缺陷在A塔内侧有600多处;C塔内侧近300处;外侧均有20多处。裂纹在筒体的纵、环缝上较少,主要分布在封头焊缝上;绝大部分裂纹分布于焊缝中心及两侧,少量在热影响区。金相观察:有晶界开裂,还有一些析出的脆性相。5. 低温分离器制造过程中焊缝内的微裂纹 某厂制造的低温分离器,其设计压力为9.9 MPa;工作压力为9.43MPa;设计温度-40℃;工作温度-35℃;介质:含CL— 的原料天然气、乙二醇水溶液;材质为09MnNiDR(NT);尺寸为Φ2200×85(筒体)/94(封头)mm。 投焊前,采用某厂焊丝、焊剂,经预热,焊后不消氢,其焊接工艺评定合格。但产品焊接时焊缝中出现大量3~5 mm的裂纹(照片),即便换焊丝、焊剂也未完全解决焊缝中的气孔和裂纹。最后从构件的拘束状况、焊接工艺等措施(预热、消氢和焊接线能量)予以解决,特别是大范围的补焊。(二)不锈钢或镍基合金设备1. 氨中和塔 某公司的中和塔,采用筛板结构分三区段。设计压力:0.06Mpa;介质:氰化物、H2SO4、(NH4)2SO4;材质:1Cr18Ni9Ti;操作压力:0.05Mpa;操作温度:80℃;规格:Ф2000 /Ф1600×10×2000mm。 该塔1987年前建成,1995年前后连续运行, 3月发现中段多处泄漏,停车后发现WM明显脱落,形成凹陷。每年修补二次,补了又漏,从人孔处流液体。(1) 泄漏原因分析调查工况、做金相检验和拍RT片。区段操作温度℃H2SO4(HN4)2SO4PH
上段30~40
5.5~7
中段70±5<1.5%< span=''><10%< span=''>2~5
下段80±5<1 %10~20%6~7
1)RT发现环缝上有大量密集的横裂,有的被覆盖在补焊焊道下; 2)多数横裂在SAW的WM上,在丁字接头附近的母材上有扇形和分枝裂纹,有的裂纹起始于点蚀处; 3)外壁的泄漏点对应于内壁塔盘角焊缝。 从检测可判断为SCC,但1~1.5% H2SO4怎么引起这么严重的SCC呢?调查发现95% H2SO4要稀释后去中和氨,用的是江水(其Cl-约80~90ppm)。 从材质、应力(自动焊残余应力大)和介质情况,中段具备SCC的条件。且环焊缝长,其纵向收缩应力大,与其收缩主应力垂直的方向形成密集的横向裂纹。(2) 修复措施 1)在中段环焊缝的一个区段涂覆耐SCC的涂料; 2)在中段的另外区段分别采用25-13和316L焊条补焊。经几个月考核,耐SCC涂料被冲刷掉,而两种焊条的补焊完好无损。 3)将中段环缝(SAW)裂纹密集处打磨出5mm深的凹槽,将人孔接管与壳体连接处,整圈打磨出坡口。用Ф3.2mm的焊条多层多道焊。经1997年修复的区段直今完好无损。2. 加氢脱硫装置中的不锈钢弯头 某石化渣油加氢脱硫装置是对高含硫渣油进行脱硫、脱氢和脱重金属。 试车过程中,在热柴油试运转阶段,发现0Cr18Ni10Ti不锈钢90°弯头多处开裂泄漏。其弯头规格Ф219×8mm。试车工况,压力:1.6MPa,操作温度:250℃;介质:轻烃;管线外部保温为高铝和莫来石纤维。试车工况正常,累计仅运行10天。(1)开裂情况 截至取试块检查:邻近环焊缝的220×70mm的区域内,发现外壁裂纹15条,内壁2条(由外壁穿透而成)。裂纹均在母材上,大多与焊缝垂直,但未与焊缝相交。(2)检测与评定 1)化学成分分析与质保书一致,符合GB/T14976; 2)质保书上的力学性能都合格,而实测的抗拉强度(特别是屈服强度)很高,延伸率较低,性能不符合要求; 3)外壁和内壁的硬度均偏高; 4)金相组织:正常应为奥氏体而弯头基体为A+F+M少,且铁素体具有明显的带状特征; 5)裂纹金相:裂纹呈典型的沿晶扩展,裂纹附近的许多奥氏体晶粒内有大量滑移线,这是不锈钢经冷变形的组织特征。 6)磁性测定:弯头的内壁、外壁和厚度方向测量均有磁性。为证实冷变形会使奥氏体产生相变,对其进行再弯曲试验。试验表明: ① 所有试样经弯曲,磁性都有不同程度的增加,变形量越大,增加越多。压缩变形引起磁性增加比拉伸变形明显,在变形量最大的第4点实测情况如下:内壁:拉伸时由1.17%增至4.30%;验压缩时由1.1%增至6.1%;外壁:拉伸时由 0.25%增至1.45%;压缩时由0.21%增至3.0%。 ② 内壁的磁性均高于外壁。 7)断口分析 断口有两个区域:一个呈半圆形的区域,属弯头制作时的开裂(其扫描电镜分析,具有层状特征的沿晶断裂,其层状结构与光镜中的带状组织有对应关系);另一个区域是弯头安装后沿原缺陷扩展的,有Cl-促进的应力腐蚀开裂。(3)裂纹成因分析 1)弯头钢材有明显的冷作硬化,表明不锈钢弯头成形后,未经固熔处理。 2)弯头钢材有磁性:弯头基体应为A,但金相分析除A外,F呈带状分布,且有M。磁性测定沿厚度方向最高达1.7%,现场测定最高在10%左右。表明制作弯头的原钢管属热轧状态,未经固熔处理。 3)18-8属亚稳定不锈钢,当继续冷到更低的温度或经冷弯形时,其中部分A会发生M 转变,即与原A保持共格,以切变方式在极短的时间内发生非扩散性相变,由于M 硬而脆,使钢材的塑性降低、强度提高(特别是σs明显上升),从而增大了变形阻力和产品开裂的可能性。(4)结论 1)压力管道因弯头开裂泄漏的事故屡有发生,对设备的安全运行造成威胁,应引起行业界的高度重视。 2)不锈钢弯头所采用的钢管没有经固溶处理,在成形过程中由于加热温度不够高和变形速度过快会产生形变诱导马氏体,使钢材强度、硬度、磁粉增加,延性和抗腐蚀性降低。因此,应加强管线安装前的弯头质量检验(特别是管件供货质量不稳定)。(5) 措施 该输油管线有100多个弯头及拾多个大小头,经检测对弯头母材上有裂纹的;磁性大于1.0%的;HB>190以及Cr含量偏低的数拾个管件进行更换,且试车成功。3.合成氨装置中的减温器 某公司合成氨装置中的减温器,设备的设计压力:4.04Mpa;设计温度:320℃;规格:Φ610×18×11096mm;材质:0Cr18Ni10Ti。 2005年9月制成,2006年12月投用。2007年4月在工艺冷凝液进口接管与法兰相连的焊缝第一次开裂(开裂区域约占焊缝总长度的3/4)并泄漏,经返修连续使用47天。7月下旬在同一接管与筒体连接的角焊缝,又发生泄漏。该设备从投用到第二次开裂,累计运行时间约70多天。操作条件:部位介质进出口温度(℃)压力(MPa)流量(Kg/h)
a预变换气进口2753.67337357
c工艺冷凝液进口1563.90/
b混合物出口275//
预变换炉出口预变换气组分组分H2COCO2N2ArCH4H2SNH3
Vol%31.8448.2211.088.030.110.010.690.02
取样分析母材局部存在较多的呈带状分布的条状铁素体,铁磁相含量最高达3.2%,局部母材硬度偏高。这表明:母材固溶处理效果不佳。导致材料的局部腐蚀和氯离子引起的应力腐蚀。裂纹以穿晶扩展并带有分叉,微观断口具有解理或准解理特征,断口上可见二次裂纹,并覆盖有大量腐蚀产物。对断口的能谱分析表明:腐蚀产物中有Cl(最高达3.91%),并有S、O等存在。这是硫化物促进下的氯化物应力腐蚀开裂。 重新制造的设备,建议选用16MnR+0Cr13,新制作的设备其焊接工艺评定焊条为A302+A132。建议不采用A132,因为18-8奥氏体不锈钢焊缝金属是不耐氯离子引起的应力腐蚀的。 18%不锈钢中Ni含量对应力腐蚀的影响(经42%MgCl2沸腾溶液试验)见下图:
4. 制氢装置 某石化制氢装置是加工进口含硫原油改扩建的主要装置。(1)15CrMo+不锈钢的异种钢接头开裂
该装置有三台下集合管(Ф1052×26×23000mm)为15CrMo,每台集合管上有108个径向连接的不锈钢的外接管(Ф168×10×250mm)。异种钢氩弧打底,用同类焊条焊满。 焊后经SR处理。试车中先后有89根外接管出现穿透和未穿透的裂纹,对带裂纹接管检验发现:1)不锈钢管内壁靠焊缝熔合区、应力集中缺陷处或点蚀处有大量密集应力腐蚀开裂(SCC)并形成穿透性裂纹,导致试车过程中的泄漏。2)镍基合金焊缝中有结晶裂纹。3)不锈钢管外壁大面积网状龟裂,属晶间腐蚀裂纹。 由于设计选用不锈钢,供材不良加上SR处理规定不当,使其内壁在高温、高含溶解氧、高Cl-浓度的试车条件下产生SCC;也使暴露在工业大气环境中数月的接管外壁出现晶间腐蚀裂纹。改造措施:324根不锈钢管全部铲除更换成Cr5Mo钢管。(2)下尾管接头的开裂
某石化制氢转化炉有324根Ф32×3.5mm的incoloy800H(Cr20Ni32)的下尾管。其一端与炉管上的加强接头相连;另一头与下集合管的内衬相连。在几次试车过程中,发现有40多根下尾管与加强接头连接处开裂或泄漏,其泄漏有两种:1)熔合线以外的母材上穿透裂纹;2)角焊缝开裂。 Cr20Ni32属Fe-Ni-Cr高合金钢,含少量Al和Ti的Cr20Ni32具有耐腐蚀、高强度和抗高温氧化等性能,而其价格远低于镍基合金。因此,不仅用于压水堆换热管,而且广泛用于石化工业。但其焊接有一定的难度。(1)焊接的难度① 焊接热裂纹敏感性高 下尾管焊接一般选用含70%左右的镍基合金, WM含Ni高,易与S、P、Si和NiO形成低熔点共晶,若这些低熔点共晶积累并形成液膜,其焊接的热裂纹倾向大。
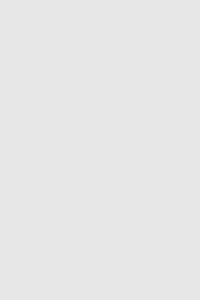
② 焊缝的气孔及未熔合 由于焊缝含镍量高,液态金属流动性差,易出现未熔合和气孔。③ 焊接接头脆化 该类合金焊接时,因焊件表面清理不彻底、溶池保护不佳、线能量过大或焊接接头过热严重都可能造成脆化。 2)结构与应力分析 下尾管的两端分别与转化炉管和下集合管相连,整个系统处于760~820℃运行。从停机到工作状态的升温过程中,下尾管要承受两种变形拘束: 一是本身温度升高而产生的膨胀; 二是下集合管温度升高(因内衬不均匀造成)产生的严重变形(轴向伸长200mm;垂直轴向约85mm),这对下尾管的应力状态影响很大。 设计计算失误,原设计下尾管较短,形状简单,吸收变形能力极差。设备在运行过程中由于变形不协调,造成的附加弯曲应力并在加强接头角焊缝附近形成应力集中。局部应力超过管材的屈服强度,从而开裂。 3)这次泄漏原因 ① 焊接质量控制不严,线能量过大,层间温度过高,放大100倍的金相照片最大晶粒尺寸达57×41mm(0.5级),表明接头脆化。 ② 原设计计算失误,下尾管只有一个90°,吸收变形能力极差,造成常温下安装的尾管在高温状态运行所需的变形补偿不足。校核计算表明下尾管两端接头处的应力超过材料的许用应力2.7倍。 ③ 多次开停车,其温度升降和压力波动,使附加应力具有一定的交变载荷性质,裂纹断口辉纹显示出大应力低周疲劳的特征。 4)措施: ① 增加下尾管(由于1602mm增至5432mm并由一个90°增至三个180°的转弯)的柔性和补偿能力;增设下集合管的外喷淋装置,以减少其变形。 ② 施焊过程中加强质量控制; ③ 将下尾管与炉管加强接头的连接,由角接改为对接,以增强接头承载能力,且可对WM进行100% RT和PT。5.制氢装置中不锈钢管开裂(1)某煤制油装置中的347H不锈钢管安装过程中的开裂 该公司引进的大口径厚壁347H不锈钢管,采用TS-347Z焊条焊接,焊后UT、PT检查未发现裂纹,但按设计要求900±10℃×(4~6)hr的稳定化后,焊缝严重开裂,肉眼可见连续和断续裂纹数百毫米。该项目不同直径和壁厚的环焊缝计200余条,已焊64个(DN≥200,t≥29mm的管道),开裂的焊口约1/3。 出现裂纹的管道规格为φ611×77,出现裂纹者均为弯管与直管连接的焊缝,裂纹多出现在焊缝立焊区域,且弯管外侧裂纹多于弯管内侧。 从裂纹的形式来看,大多数裂纹都是横向裂纹和纵向裂纹,也有少量微裂纹(打磨1mm可消除)。安装部门分析,微裂纹可能是焊缝结晶过程中产生的。取样分析情况如下: 1)稳定化处理后,铁素体含量明显减少,表明铁素体发生转变焊后状态的铁素体含量 %稳定化处理后的铁素体含量 %
按化学成分计算仪器测量纵向裂纹试块横向裂纹试块
9.811.781.033.02
2)光学显微镜观察 裂纹均沿焊缝金属中的F或F与A晶界开裂。这说明:在稳定化处理应力松弛过程中,因F发生转变或碳化物析出而变脆,不能满足蠕变变形的需要,而导致局部开裂。 3)扫描电镜观察 对纵向和横向裂纹试块沿裂纹打开,扫描电镜显示:断裂面沿焊缝柱状晶开裂,属于脆性断口;断口上显示为许多小坑状微孔,微孔面存在若干白色块状物,采用能谱分析,这些白色块状物Nb含量极高。而这种裂纹与铁素体相中的高Nb的金属间化合物(如σ相)或在晶界析出了NbC有关。 经稳定化热处理的断裂面。类似于蠕变断裂时的形貌,这认为是焊接再热裂纹的特征。4)试验结论 根据环缝的制造工艺和裂纹的形貌特征,可以确认神华厚壁大口径347H管环缝是再热裂纹。这种裂纹具备以下条件: ① 焊后经过再次加热(消除应力退火,稳定化处理等),裂纹产生的温度区间通常低合金钢为500~700℃,高合金钢则在700~900℃。 ② 这种裂纹在低倍放大观察为沿晶间断裂;在高倍下观察,断裂面上存在断裂空穴,类似于蠕变断口的形貌。 ③ 存在大的残余应力和应变条件在大拘束度的厚件或应力集中部位易于产生。 5)防止再热裂纹的建议 表明:焊缝经稳定化处理后,裂纹沿铁素体或铁素体-奥氏体晶界开裂,而且裂纹断口上析出物和金相试样上铁素体组织上能谱分析显示,C、Nb含量很高。为了防止347H管焊缝再热裂纹,从焊材和施工工艺方面提出以下建议: ① 减少焊条中化学成分C、Nb含量;② 减少熔敷金属铁素体含量(约6%);③ 保持层间温度(200~300℃),减少收缩应变;④ 最后3~5层采用对稳定化处理不敏感的E308L焊条焊接,防止从外侧启裂;⑤ 如果采用308L焊条焊接,将稳定化处理温度提高到950℃以上。(2)某公司合成氨装置不锈钢管线使用后的开裂该公司合成氨装置(凯洛格箱式炉转化流程),2005年改扩建,为提高负荷,在一段转化炉前增加了预转化炉,其间连通管(φ356×22mm)的材料为TP321H。管线的设计压力为3.9MPa;操作压力为3.9Mpa;设计温度为675℃;操作最高温度为650℃;介质为高温天然气+蒸汽。投用两年后,NG-04109-14”管线的直管与弯头连接焊缝开裂。从外侧看:西边裂纹长约80mm,打磨达到200mm;东边裂纹长约100mm,打磨两端也扩展,均为穿透性裂纹。经修复补焊后,已运行,解决方法:(1)从管线位移、支撑布置来看,开裂部位可能存在较大的附加弯曲应力,支撑欠合理;(2)管件固溶处理效果欠佳,金相组织中存在少量的形变马氏体,并且条带状聚集分布TiN夹杂物和条状硅酸盐夹杂物均超标;(3)施工单位采用φ219×23mm的TP321管进行焊接工艺评定。评定报告为V型坡口,氩弧焊打底(焊材为TGF347,电流90A;电压10~12V);填充和盖面为手工焊(φ3.2mm的A137,电流为80~120A;电压为20~25V)。坡口底部的1~4层为单道焊;填充和盖面的金属5~8层为双道焊。但后经解剖的焊接接头,其焊层厚为4~5mm。(4)焊接原始记录不详,一些焊缝成形较差,局部焊缝咬边严重;(5)施焊弯头和直管的焊缝,拘束应力大,焊缝结晶时,承受较大的拉应力。该处接头冷却时趋于三向散热(直管对接焊时为两向散热),若冷却速度较快,在拉应力作用下,容易产生RT检测灵敏度检测不出的微裂纹;(6)泄漏处是弯头和直管的连接焊缝,从焊接熔池结晶时形成的焊波来看,裂纹沿双道焊的两焊道之间扩展。坡口根部已经破坏,其特征不明。这至少表明:双道焊的焊缝交界处熔合不良,这会成为焊接接头承载时的薄弱环节。若坡口制备不佳、氩弧焊打底时,其根部保护不良、焊接工艺规范或焊道布置不当,会在焊缝的根部或内部形成微裂纹或局部熔合不良。这些隐患在装置运行时逐渐扩展,以至形成穿透性裂纹,最后导致介质泄漏。(7)是否由于材料在650℃敏化温度区域中运行,导致不锈钢的脆化?由于检测数据不足,还无法确定。(8)制氢装置中的321H不锈钢管使用后的开裂 某公司的加氢裂化装置有7条约高压临氢管线,2005年4月投用,2008年对管线检测,数拾处焊口出现裂纹(主要集中于焊缝金属;也有在熔合线和热影响区,多为纵向,)。经焊接返修投用。2010年再次对其检验(PT、RT),有很多裂纹。1)金相检查 ① 微观检查裂纹均在焊缝金属上(有横向、纵向;均沿晶开裂,扩展到熔合线附近中止); ② 在焊缝弯头侧热影响区的坡口上,局部有沿晶的微裂纹,近焊缝区母材局部有形变诱导马氏体;2)硬度及铁磁相的测试① 对弯头侧熔合线附近的坡口的硬度测试表明:局部区域硬度较高; ② 铁磁相测量表明:弯头的内弯处的母材局部磁性较高,在该处组织中有形变诱导马氏体存在,这说明弯头在弯制过程中的温度偏低;③ 焊缝金属是经捶击的焊道硬度值和铁磁相含量均偏高。3)结论① 焊缝金属上的多为热裂纹,局部有再热裂纹;坡口截面焊缝热影响区的属液化裂纹;② 导致开裂难以返修的主要原因是建设初期施工,工期紧,天气又冷,施焊不当,导致焊缝金属的内在质量较差(可能有微裂纹),在运行期间以及开停工期间,临氢管道的焊接接头渗氢脆化,使原有的缺陷进一步扩展,给后续修复造成困难。6. 某公司脱乙烷塔使用中泄漏 设计压力:2.47 MPa ;工作压力:2.35 MPa ;工作介质:C1-C12; 设计温度:-80℃(气相进出口温度:-50~ -60℃;液相进口温度:-20~ -50℃); 材料:0Cr18Ni10Ti;壁厚:16/12mm。 2005年11月28日19:00点,发现脱乙烷塔重沸器回油管线塔体侧法兰焊缝泄漏,喷液长度约有10-15cm。为此,停运40万t/a装置分馏系统(降压、排液、放空、置换)。 29日对泄漏处焊后检测,又发现焊缝周围有裂纹,补焊检测合格后,准备恢复生产。对乙烷塔进气,加压到1MPa时,重沸器回油管线法兰焊缝两侧泄漏,法兰短节轴向开裂。 11月从29日晚到12月16日经厂检验人员及锅检所(对塔完成100%检测)检测,对失效的法兰进行的分析表明:(1)钢中Cr的含量偏低;不含Ti,应属于0Cr18Ni10;(2)有的法兰母材中有少量的马氏体,晶界上碳化物析出;(3)裂纹从焊缝熔合区开裂,向母材扩展,呈沿晶特征且有分叉;电镜观察断裂以沿晶为主,且有二次裂纹,属于沿晶脆性断裂。12月17日准备恢复脱乙烷塔生产,18:00开始置换试压,20:30塔压力升到0.9MPa时发现塔顶部人孔焊缝漏气,经检查整个一圈焊缝都有裂纹。维修时由于环境温度不在5℃以上,另外,修完后整塔要进行水压试验,水温不能保证(要求不小于30℃,保压不小于4小时?)。
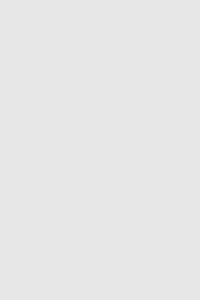
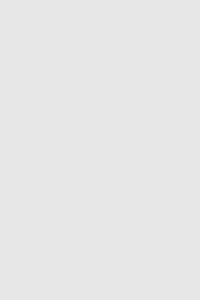
欢迎加入化工设备圈
本站仅提供存储服务,所有内容均由用户发布,如发现有害或侵权内容,请
点击举报。